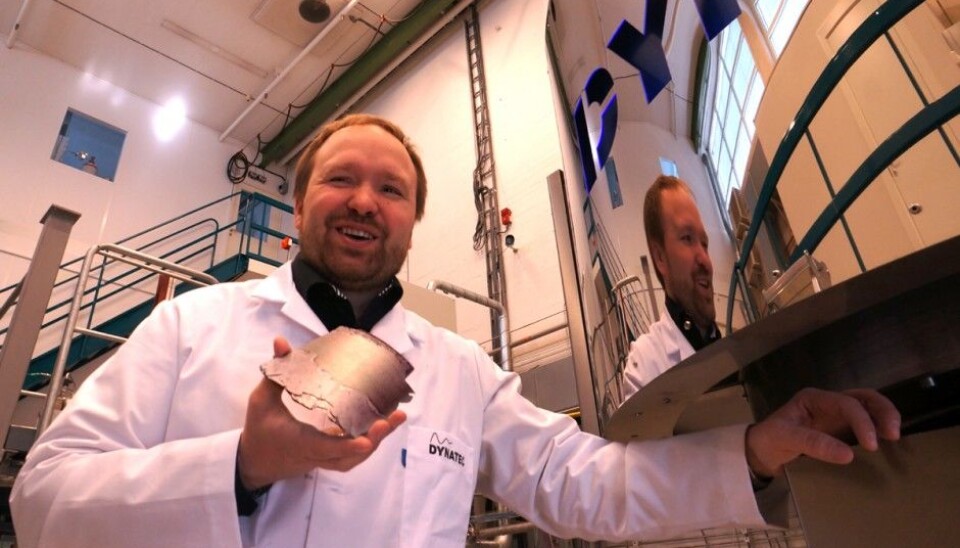
Speedy production of silicon for solar cells
A growing solar cell industry needs cheaper silicon in increasing amounts. A centrifuge developed in Norway could supply it.
A centrifuge is mounted in a large hall at the Institute for Energy Technology (IFE). You wouldn’t want to spin-dry your jeans in it. Centrifugal forces of this machine, produced by Dynatec Engineering, would destroy the fabric.
Dynatec’s Werner Filtvedt is reluctant to tell us exactly how fast the machinery spins. He’s a researcher and section head. Much of the technology is still an industrial secret.
The purpose of this centrifuge is to feed an increasingly hungry solar cell industry with purer and cheaper silicon – as expeditiously as possible.
“We amass silicon as much as 40 times faster in this centrifuge reactor than in a traditional reactor,” says Filtvedt.
Scalding hot centrifuge
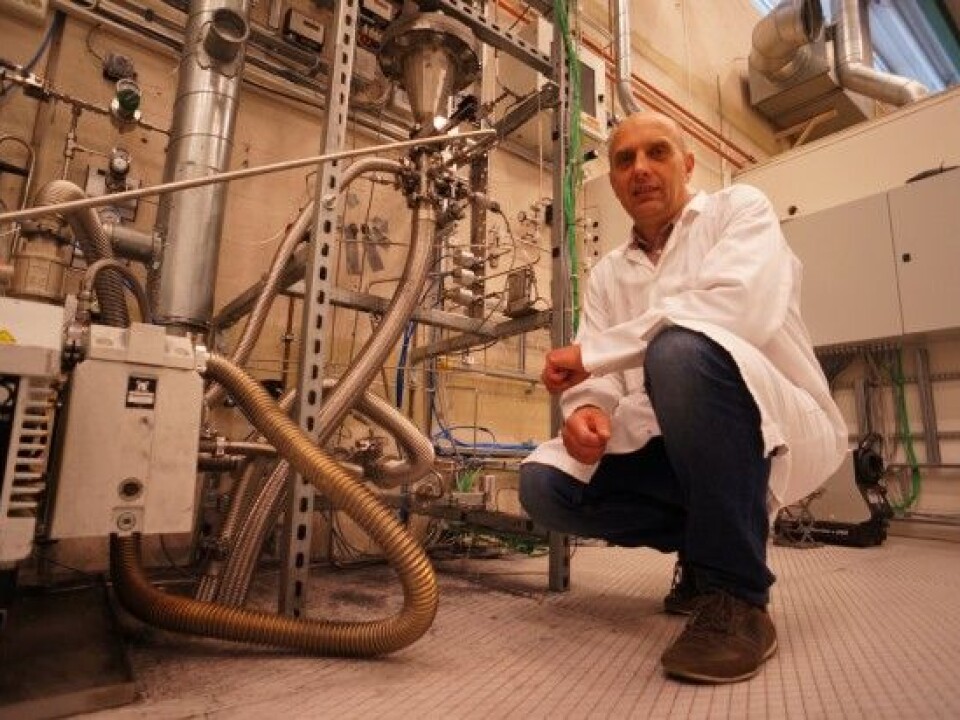
This is not ScienceNordic’s first visit to a Dynatec centrifuge. Two years ago we visited the same hall and saw its smaller predecessor.
This prototype showed that the method worked. The new centrifuge is meant to show that the method can be used on a larger, industrial scale.
“We will also extract the silicon it produces without cooling down the centrifuge,” says Filtvedt.
The temperatures it operates with are another reason why the Dynatec centrifuge would be bad for your laundry. Your jeans would burn to a crisp. It takes fierce heat to produce silicon.
Slinging out silicon
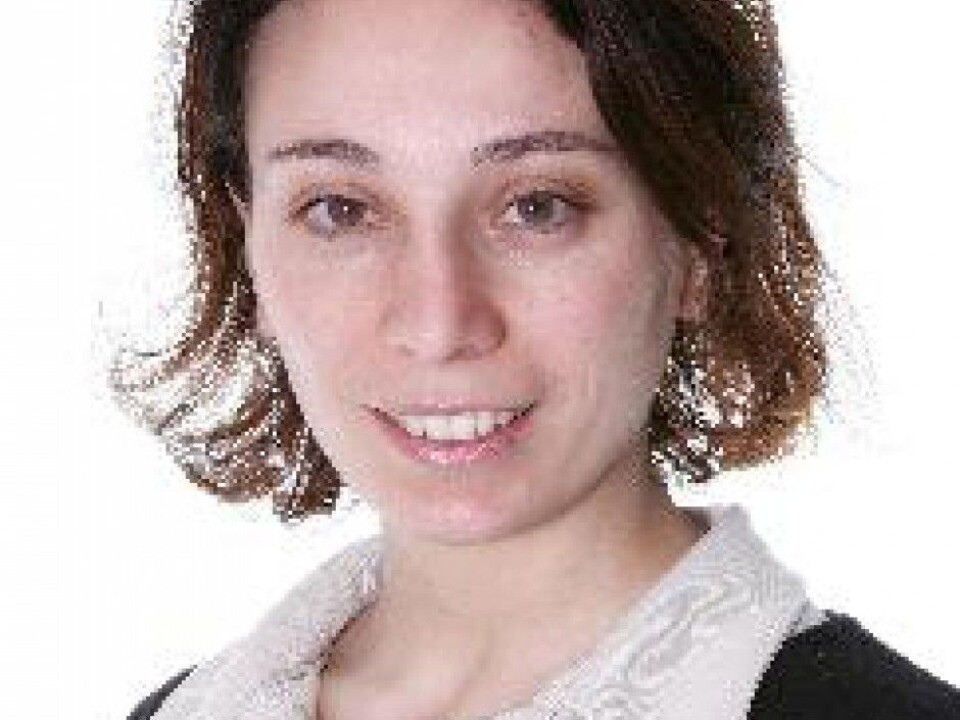
Silane gas is piped into the centrifuge. The gas is extracted from quartz and other rock types that contain silicon. Most producers of super pure silicon now use silane gas or comparable gasses in the process.
A silane molecule consists of one silicon atom bound to four hydrogen atoms. The bond breaks when the gas is sufficiently heated up. The hydrogen and silicon atoms go their separate ways.
This is where the centrifuge is needed. Silane gas and silicon have greater mass than hydrogen. In a centrifuge it is slung out towards the walls, where the silicon deposits.
The lighter hydrogen gas accumulates in the centre of the tank and can be pumped out.
Heat harvesting
The scientists at IFE and Dynatec have found a way to extract the silicon while the centrifuge is still hot. This is called heat harvesting. It eliminates the waiting time between cooling and reheating.
“First we blow in a little pure silicon powder which spreads out on the walls of the centrifuge. It has a similar function as Teflon in a frying pan. It allows the additional silicon which deposits on the walls to peel loose, even if the centrifuge is hot,” explains Filtvedt.
Small pieces
Pieces of silicon, shaped by the curved wall, can thus be removed. The force of the centrifuge makes the silicon accumulate in strips which are easily broken apart into smaller pieces.
Such small pieces are easier for solar cell producers to melt. This is an advantage over the traditional Siemens method of silicon production, which involves deposits of the silicon on an extremely hot tube.
The purer the better
The thin peels of silicon formed on the walls of the centrifuge provide a bonus effect. They keep the wall materials from contaminating the silicon, which should be kept as pure as possible.
“The industry demands this because the purer the silicon the more efficient the solar cells,” says Filtvedt.
As for now, the Dynatec method is not making silicon as pure as that from the Siemens method. But Filtvedt thinks future improvements will solve the problem.
Fluidized bed
In any case, the Dynatec method also produces purer silicon than an alternative method currently used by the industry. In the alternative, silane gas is blown upwards through silicon spheres in a heated tube.
These tiny balls float on the gas and act like a fluid at the bottom of the chamber.
The process is called a fluidized bed.
Silicon collects on the spheres in this floating bed. They aggregate, more or less like hail in a thunder cloud. The fluidized bed method is used by producers including REC.
“The fluidized bed technology is cheaper than the Siemens method, but there is more waste in the form of dust. We are working to improve it,” says Hallgeir Klette, a department engineer at IFE’s solar energy centre.
Taking a loss
The Dynatec method still has a way to go before it being utilised industrially. The next step is to build a prototype that can be tested by industrial producers.
“Many solar cell producers are now running deficits. The competition is fierce. The only ones making money are using the fluidized bed technology. The centrifuging of silane gas will help make the industry profitable again,” says Filtvedt.
More markets
“This is a fascinating project, but as the Dynatec method produces purer silicon than the fluidized bed, it should be used in other markets than solar cells,” comments Marisa Di Sabatino.
Di Sabatino is an associate professor at the Norwegian University of Science and Technology’s (NTNU’s) Department of Materials Science and Engineering. She points out that solar cells do not require such a pure form of silicon as, for example, computer chips and other types of electronics.
“The price of pure silicon for solar cells has dropped to a tenth of its price at the turn of the millennium. Elkem produces silicon with a lower degree of purity but which is just as good for solar cells. Still, they also struggle to be price competitive,” she says.
“The Siemens method was originally developed to produce silicon for electronic devices. The process demands much more energy than the Elkem method. But the silicon yield is far purer.”
¬“If the Dynatec method could turn out silicon that is equally pure at a lower price it would dominate the market. In any case, it’s an advantage for the silicon to be produced in Norway, where the energy is cheap and mostly renewable,” says Di Sabatino.
Little gained by leaving the fluidized bed
“Few producers currently make polysilicon from silane gas,” writes Harry M. Rong in an e-mail to ScienceNordic’s Norwegian partner, forskning.no.
Rong leads the product development and innovation at Elkem Silicon Materials. Polysilicon is the name of the pure silicon used by the solar cell industry, amongst others.
Rong points out that these producers have already developed ways of rendering silicon using the fluidized bed technology. He thinks the gains would be minimal if the fluidized bed method were to be exchanged for Dynatec’s centrifuge.
Dependent on silane production
On the other hand, like Di Sabatino, he thinks that the centrifuge could be of interest for those who currently use the Siemens method. But a problem remains – finding or setting up facilities that produce silane gas satisfactorily.
“There are companies that have the technology, but as far as I know they aren’t selling the technology,” writes Rong.
-------------------------------------
Read the Norwegian version of this article at forskning.no
Translated by: Glenn Ostling