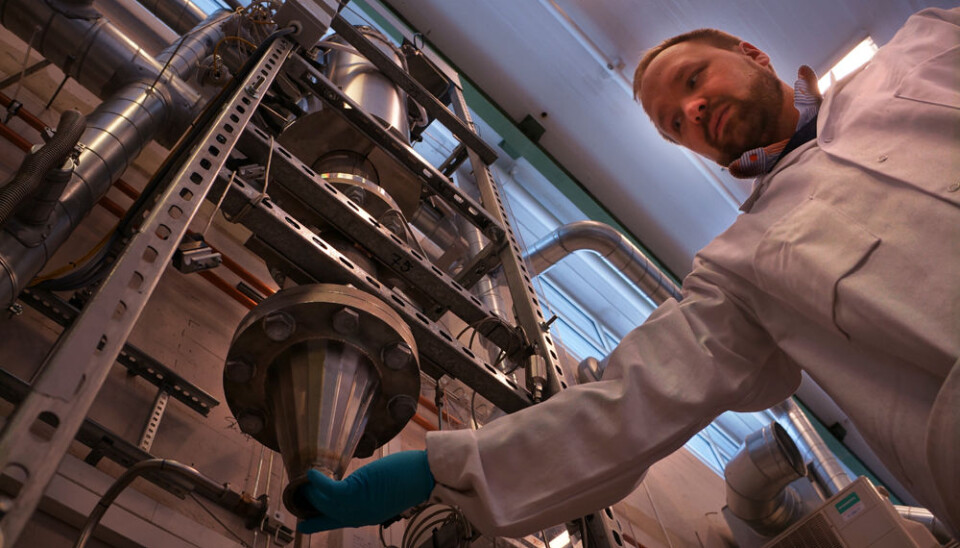
A silicon sprinkle for electric cars
The driving range of electric vehicles can be increased by 25 percent if silicon replaces graphite in their batteries. A new manufacturing method creates nanopowder sprinkles that can do the job.
Denne artikkelen er over ti år gammel og kan inneholde utdatert informasjon.
A heavy gas sinks down through a vertical metal cylinder at the Institute for Energy Technology (IFE). The gas is silane, a compound of hydrogen and silicon (SiH4).
It’s hot inside the pipe, nearly 1000° C. That’s too hot for silane. The heavy molecules break apart.
Four hydrogen atoms are split off, leaving a single atom of silicon. The silicon atoms are attracted to each other and bind. Tiny flakes of nanopowder drift down the cylinder − a silent sprinkling of silicon.
Werner Filtvedt, Trygve Tveiterås Mongstad and Jan Petter Mæhlen can fish this agglomerate powder of silicon out from the base of the cylinder. And then they have something that may make electric cars more attractive than they are today.
Rigorous specifications
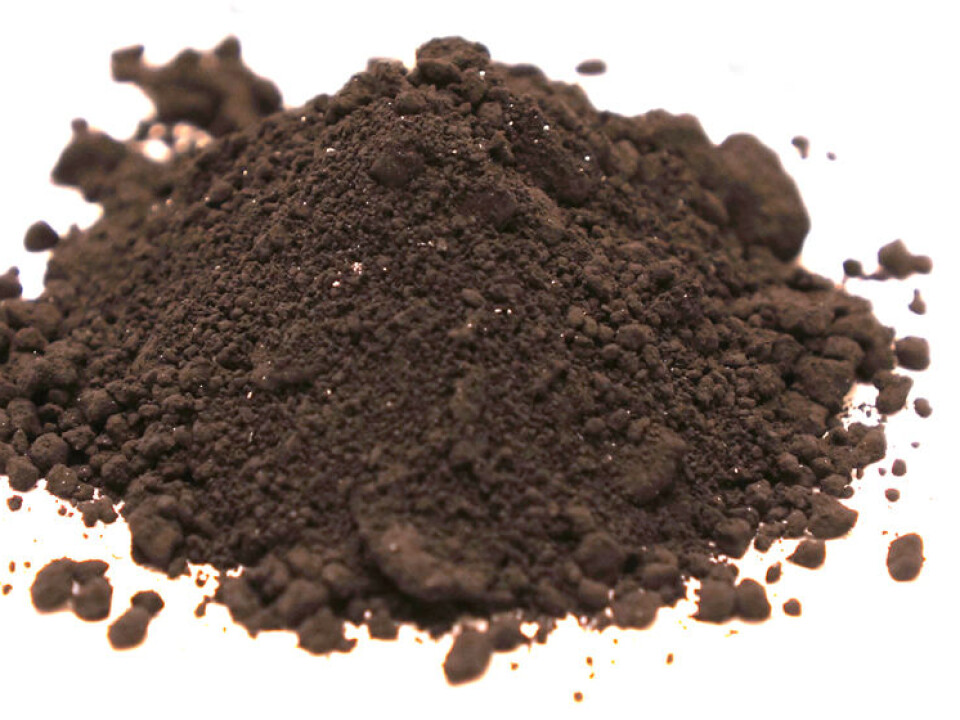
The silicon powder can replace graphite as the positive electrode − the anode − in lithium-ion batteries. Silicon has characteristics that enable the battery to store more energy than its more conventional progenitor.
But these properties also create special problems, so the powder has to meet stringent standards.
The problems are linked to the way a battery creates electricity. This occurs when lithium atoms migrate from the anode to the negative electrode − the cathode − of silicon inside the battery.
Fine and even
Silicon has ten times graphite’s capacity for taking on lithium. This means the battery’s ability to generate electric current can be increased by 25 percent.
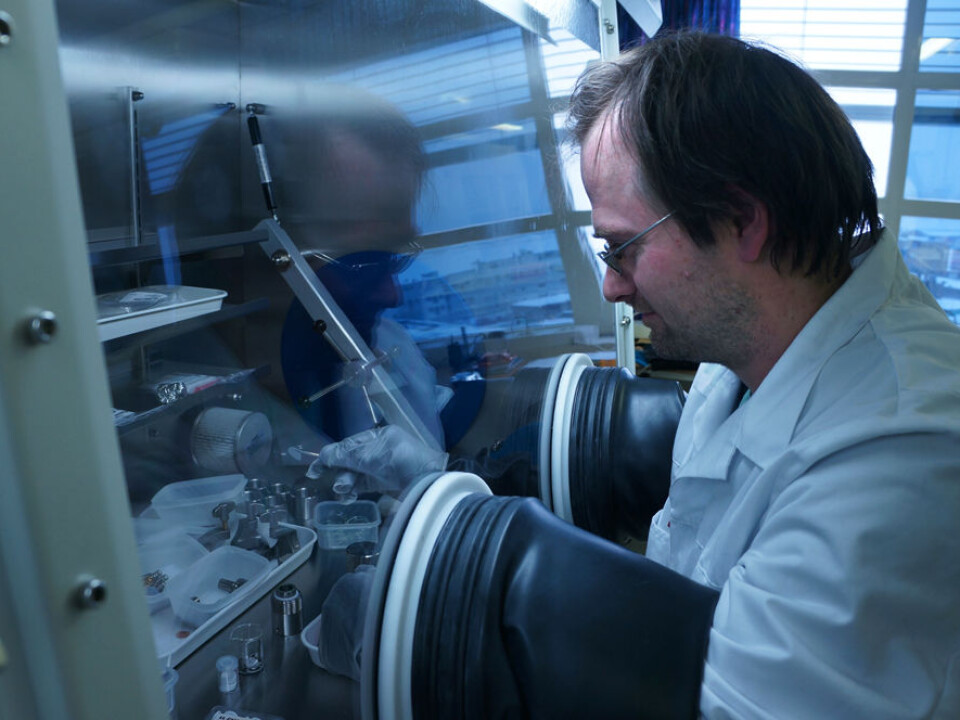
But ten times as much lithium in the electrode means it also has to expand more, quadrupling in size.
If the grains of silicon are too large or uneven in size and shape, the expansion creates tension in the electrode, and it can break apart.
Consequently, the particles that fall like fine snow out of the metal cylinder at IFE have to have just the right qualities.
They must be very tiny, about one-ten thousandth of a millimetre in diameter. The smaller the silicon particles, the larger the surface area is where the reaction actually takes place. This increases the electrical current from the battery.
Several on the launching pad
The metal cylinder is called a freespace reactor. It gets its name because the silicon powder is created during a free fall through the vertical pipe. The freespace reactor was devised at IFE by Filtvedt and his colleagues.
They are not the only ones who are developing silicon for lithium-ion batteries. The Norwegian firm Elkem has recently launched its own method of manufacturing silicon powder, independently of the scientists at IFE.
IFE and Elkem are now cooperating on a third method, entailing an electrode made from a mixture of silicon and graphite.
Several electric vehicle manufacturers are working on the development of batteries that use silicon in the cathode.
Intense research is being carried out around the world in this field. Despite a number of promising breakthroughs, the IFE researchers say the goal of affordable, mass produced silicon batteries is still far off.
Basic research
But Filtvedt and his colleagues think IFE at Kjeller has the staying power - or should we say powder - needed to play an important role.
The industry is primarily focused on silicon for development of an efficient, marketable product. Once that is achieved, some of the impetus for research and development will be lost.
IFE can take development further. With the institute’s commitment to basic research, it can study processes more fundamentally and continue work on more of a long-term basis.
The freespace reactor is an example. Battery production for EVs is a growth industry and its expansion provides opportunities for independent research institutes such as IFE.
---------------------------
Read the Norwegian version of this article at forskning.no
Translated by: Glenn Ostling