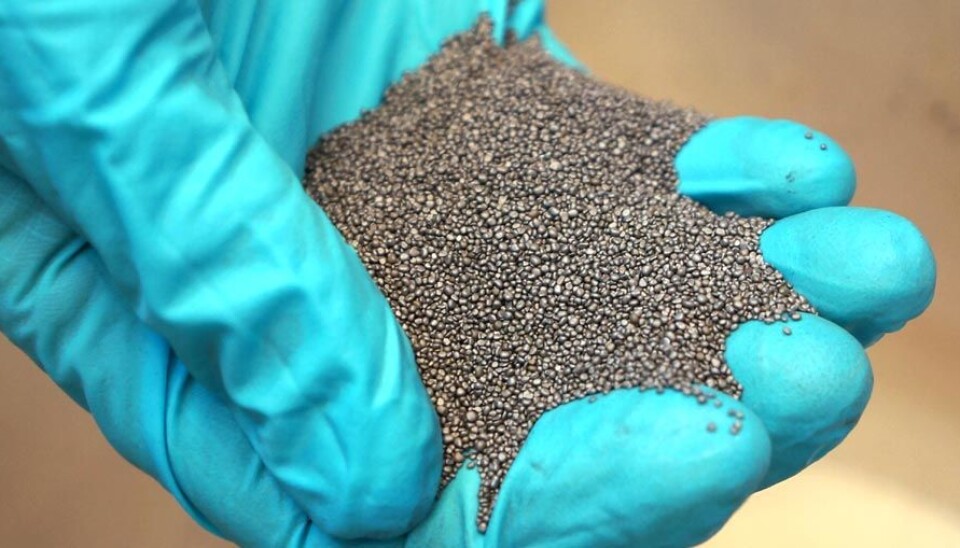
Taking silicon for a spin
Scientists sling it outwards in centrifuges, or whip it up like hot hailstones. They are finding novel ways to make super pure silicon quickly and efficiently.
Denne artikkelen er over ti år gammel og kan inneholde utdatert informasjon.
Silicon has to be very pure for use in solar cells. No more than one foreign atom is permitted among every million silicon atoms.
It takes plenty of energy to produce pure silicon – 100 kilowatt hours per kilo. Faced with soaring electricity costs and falling prices for solar cells, manufacturers have been running into the red.
Silicon producers are desperate for solutions to this fundamental problem, according to Werner Filtvedt and Trygve Tveiterås Mongstad of the Institute for Energy Technology (IFE) at Kjeller, on the outskirts of Oslo.
They think they’re onto a solution.
Centrifuge
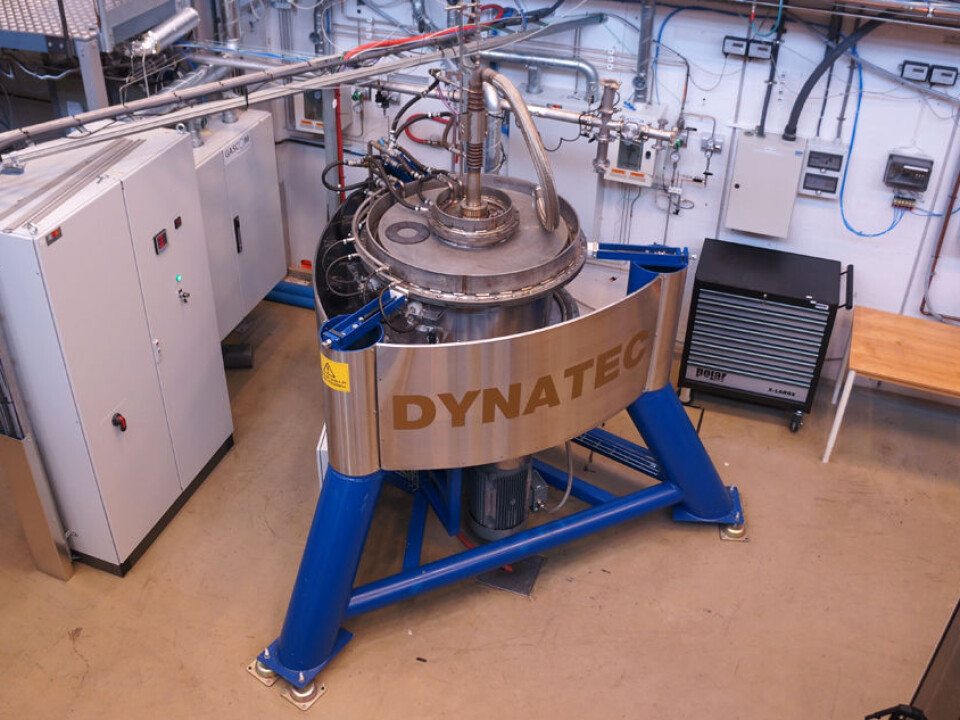
A drum stands on three stout blue metal legs in a laboratory hall. The name Dynatec is displayed in large lettering on part of the brushed aluminium cover.
Dynatec is a Norwegian firm that is developing technology with IFE. The drum looks something like a washing machine on steroids. That isn’t far off the mark, because it is a centrifuge.
Researchers have found that the centrifuge can help them reduce the power consumed by silicon purification by 90 percent.
Silicon from gas
The standard power-hungry industrial approach to making pure silicon is called the Siemens process.
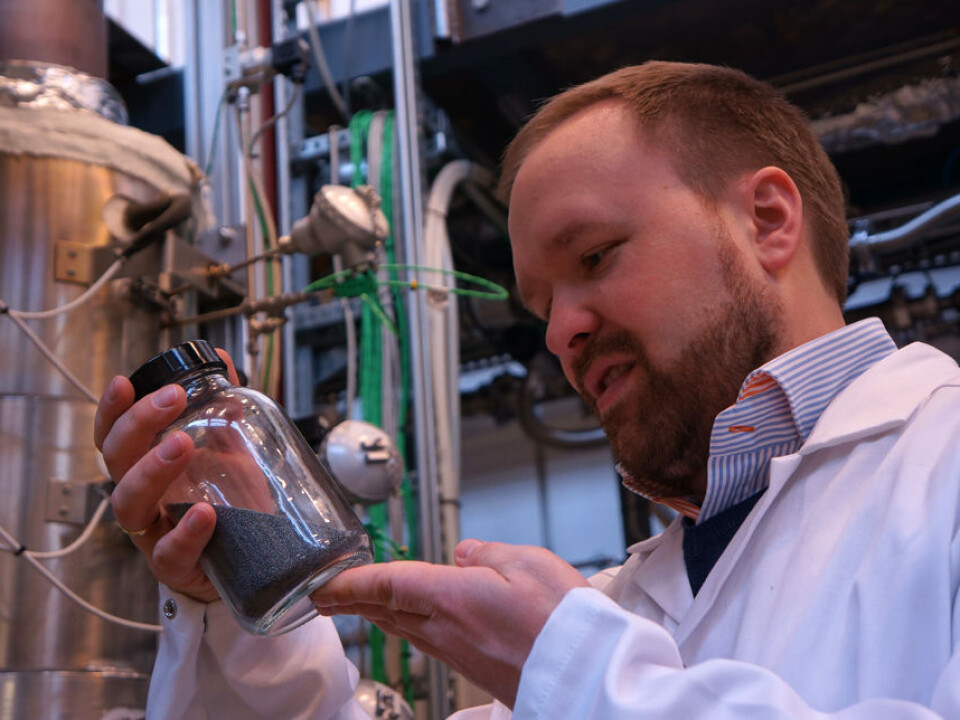
Gas containing silicon is pumped into a Siemens reactor. The most common gas to use is called silane, a molecule which consists of four hydrogen atoms and one atom of silicon.
A curved heating element made of silicon is located in the middle of the Siemens reactor. The heat energy makes the hydrogen atoms lose their grip, leaving pure silicon on a hot tube.
Grilling element in a freezer
The actual process is called Chemical Vapor Deposition (CVD).
The heating element is very hot, around 900° C. The walls of the reactor have to be kept cooler, just around 250° C. This keeps silicon from depositing on the walls.
Maintaining such a big temperature difference gobbles up energy. Filtvedt and Mongstad compare the Siemens reactor to having your oven’s grilling element mounted in your freezer.
Inside-out
When the scientists developed their CVD reactor in cooperation with Dynatec, they took the Siemens reactor as their point of departure and then turned it inside-out.
This means that the silicon is deposited on the outer walls rather than in the middle of the tank.
In the IFE reactor, the outer walls are the ones that are scorching hot. This is where silane gas is split into silicon and hydrogen.
But the centre of the tank is also hot. The silane gas could form small dust-sized particles here. To avoid that problem, something has to be done to get the silane entering the chamber out to the walls as quickly as possible.
Slinging silicon gas
This is where the centrifuge comes in. The entire tank rotates. Silane is a relatively heavy gas compared to hydrogen, which helps make the new process work. As the tank spins, silane is hurled out toward the walls and the silicon is deposited there in thick tubes.
The lighter hydrogen gas concentrates in the middle of the tank and can be pumped out.
Filtvedt and Mongstad emphasise that their technology isn’t ready for the market yet. But they claim to be the only ones in the world to have such a device so far.
Like hail in a thunder cloud
The IFE scientists have another trick up their sleeves that can pan out sooner: A reactor that produces silicon spheres the size of small hailstones. This device is being developed in collaboration with the solar cell manufacturer REC, and others.
The researchers compare this reactor to the way hail is formed in a storm cloud. Small particles of ice are repeatedly lifted by updrafts inside the cloud and accrete – get larger and larger.
In a reactor these updrafts consist of gases that are blown from below between balls of silicon. They move around freely, acting like a liquid in the bottom of the tank. The process is called a fluidized bed.
Silane gas is pumped into the tank and causes the updraft. Heating elements in the walls keep the silicon granules hot. This splits the gas and silicon is deposited on the surface of the balls. These silicon particles accrete like hailstones.
Hard to manage
Fluidized beds are used in a variety of industrial processes today.
When the IFE scientists use it to create pure silicon, they save nearly as much electricity as they do with their centrifuge.
But the fluidized bed technology has its challenges. Temperatures inside the tank are uneven.
This varies the reaction rates and the process is hard to control.
If that weren’t bad enough, the silicon hailstones batter against the walls, accumulating impurities. A lot of work has been done to find solutions to these problems.
Revolutionary potential
The silicon reactors are being developed in close cooperation with the industry. However, research at the Institute for Energy Technology is more basic than anything that the financially-pressed solar cell manufacturers can spend time on.
So Werner Filtvedt and Trygve Tveiterås Mongstad at the Institute for Energy Technology have high hopes of contributing knowledge and developing technology that can revolutionise production of super pure silicon for solar cells.
Translated by: Glenn Ostling