Opinion:
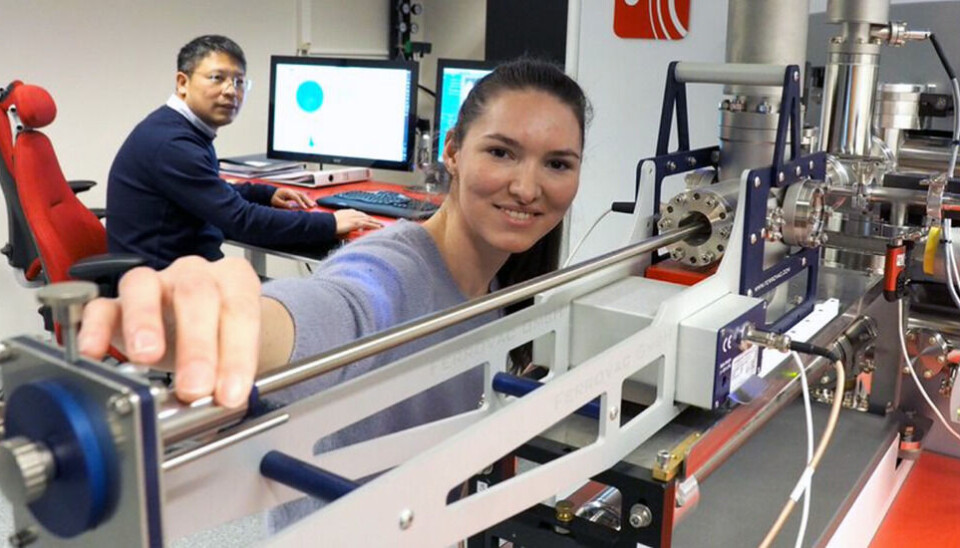
Would you drive a car built from recycled materials?
Norwegian industry is shifting towards a greener future. But what does the transition to a greener economy really mean for industry and for consumers?
Let’s take cars as an example. When we wreck a car, usable parts are taken out and reused. Materials that can be remelted are sent to recycling.
A lot of a car’s parts contain valuable metals (including the battery that has important rare metals) that hold great potential for a new life. The degree of recycling depends on how the car parts are produced.
The green shift means that we slowly but surely need to get used to the idea that the products we buy are not “new”, but consist of materials that have been given new life through recycling. The latest report from the United Nations’ Intergovernmental Panel on Climate Change (IPCC) is crystal clear that immediate and major reductions in greenhouse gas emissions are necessary in order to achieve the Paris Agreement goal to limit the earth’s temperature increase to 1.5 degrees Celsius.
For industry, this means transitioning to manufacturing low-carbon products. More products need to be recycled, and production has to be adapted to a world where things are reused, either as the same as the original product type, or remelted and reused for new purposes.
The green shift
The goal is to maintain the value of products, materials and resources for as long as possible, which aligns with the principle of a circular economy. The idea is that all manufacturing should take into account the product’s lifespan and recycling possibilities.
Another important factor is high product quality. We need products with a long shelf life that do not need to be replaced often. Longer product life will contribute to the green shift.
The transition to greener processes in the metal industry has been going on for some time already, but the awareness of the great potential for further reducing emissions is now growing.
Norwegian (and international) metal-based industries must increasingly comply with national and international rules and requirements for greater use of recycled metal in its materials and products.
The reuse of materials is essential for the green shift
Better systems and routines for collecting and sorting scrap metal are important, but it is also critical and necessary to develop new metal alloys and products that are designed to be recycled.
New technologies (process and material solutions) and innovations that enable greater reuse of scrap metal are absolutely essential in the green shift. For example, 75 per cent of all aluminium produced in the world is still in use and represents a major resource for the aluminium industry, both in replacing and in supplementing the primary production of aluminium. Remelting requires only five to seven per cent of the energy required for primary aluminium production.
Finding new and greener manufacturing methods requires a lot of new knowledge. Research and industry need to work hand in hand for a rapid green shift. Funding schemes for research in Norway (e.g. the Research Council of Norway’s “Green Platform”) and internationally (e.g. the EU’s “Green Deal”) are now aimed at projects that have sustainability as their fundamental objective.
Innovative measures will facilitate increased knowledge. Ensuring that all the new knowledge is actually used in the industry and becomes part of the circular economy is also key. To this end, research organizations and industry must collaborate closely.
Researchers and industry partners must work together
NTNU and SINTEF have established SFI PhysMet, a centre for research on physical metallurgy where researchers and industry partners work closely together. The centre is one of the Research Council’s centres for research-based innovation (SFI).S
Physical metallurgy can be defined as the ‘art’ of making useful products from metals. The field encompasses the study of the properties of metals and alloys, such as mechanical strength and forming properties. The overarching goal of SFI PhysMet is to help Norwegian metal-based industries shift to more sustainable materials, processes and products.
SFI PhysMet is collaborating with the automotive industry to produce car parts with lower CO2 footprints. The centre is also working to create sustainable metal-based solutions important for the development of offshore wind turbines, the construction of large bridge structures that can replace the ferry on the E39 highway between Trondheim and Kristiansand, and new processes for making materials and alloys better suited for recycling and recovery.
The interaction between research and industry is important for achieving the green shift. In the end, however, it is consumers who will make use of all the “green” products. Down the road we may all be driving cars produced completely from recycled materials.
We can probably expect the recycled products to be at least as good as today’s products. The difference is that the new production methods will contribute to the green shift and a safer future for our planet.
This article previously appeared in Adresseavisen, Trondheim’s regional newspaper.
Share your science or have an opinion in the Researchers' zone
The ScienceNorway Researchers' zone consists of opinions, blogs and popular science pieces written by researchers and scientists from or based in Norway. Want to contribute? Send us an email!